HP/LP SEPARATORS & INTERNALS
Technical Specifications
HP Separators
The primary separation devices, high pressure separators are mainly used for the segregation of three phases such as gas, water and oil. Gas, water, and oil components from the initial inlet stream will come out of the oil wells and eventually move to the low and medium pressure separators before they reach the stock tank.
High pressure is required for the lighter components in the liquid phase for stabilizing, which also results in a faster retention time. In addition to that, the separation of liquid from one another also occurs at a rapid pace due to this. Nevertheless, manufacturers will also have to maintain high pressure to the optimum level in order prevent the lighter components in the liquid phase from ending up at the outlet gas stream.
LP Separators
Manufactures use the tertiary separation devices, low pressure separators after completing the primary segregations of gas, water and oil. Low pressure is a necessary requirement for the efficient separation of the liquid components that are present in the liquid phase. In addition to that, it also ensures that the water is made pure as much as possible in order to make it eco-friendly.
Manufacturers also adopt necessary steps to maintain the low pressure at an optimal level in order to prevent the stabilization of the lighter components in the liquid phase. Failing to maintain the low pressure level to optimum will result in less efficient liquid-liquid separation, which is the reason why you should seek the help of our experienced crew members. The configuration of LP separators is almost similar to that of Hp separators but it can be easily customized as per the process requirements of the customer or the project.
Three-phase Separator
Three-phase Separators are mainly used for the segregation of the three phases of oil, water and gas. The main component of Three-phase Separators is an inlet deflector. Manufacturers implement the use of an inlet deflector for minimizing the momentum of the inlet stream.However, inlet deflectors also help manufacturers to easily separate the gas from the liquid phase at a rapid phase. Two wave breakers or perforated baffles are also used in the process to eliminate the chance of wave formation within the vessels. The use of this wave breakers ensure that the liquid –liquid separation is well-organized and it also makes sure that the gas distribution is consistent and uniform.
In addition to that, the presence of weir plates is crucial to the process,as it ensures that the levels of water and oil is properly maintained in such a way that the liquids gets segregated properly and they gets also drawn by the corresponding control valves at respective sumps. On the other hand, the mist extractor which is placed right at the outlet gas nozzle for combining the fine droplets that are scattered in the gas phase eventually becomes entrained right at the separators liquid phase.
An inlet deflector can be easily designed in the form of a cyclone inlet,wave breakers, defector baffle, vane type inlet device or de-forming plates for increased momentum. The weir plates are usually placed at the vessel’s bottom while the perforated baffles are located at optimum distances in order to make sure that the segregation happens at a rapid pace. It is significant to note that the outlet mist extractor can also be designed in the form of vane type demisters, mesh demisters but they are available to customers in the form of cyclones.
In addition to that, the separators are also available in both vertical and horizontal vessel configurations. However, the horizontal three phase separator is undoubtedly the ideal choice for Gas handling processes,which needs more space and simple service. On the other hand, the vertical three-phase separator is the perfect choice for solid handling applications that needs less space and harder service. Our company manufactures and supplies vessels with internals and we also offer initial design for initial design for FEED stage evaluation, de-bottlenecking existing vessels and rating of existing designs.
Separator Sketch
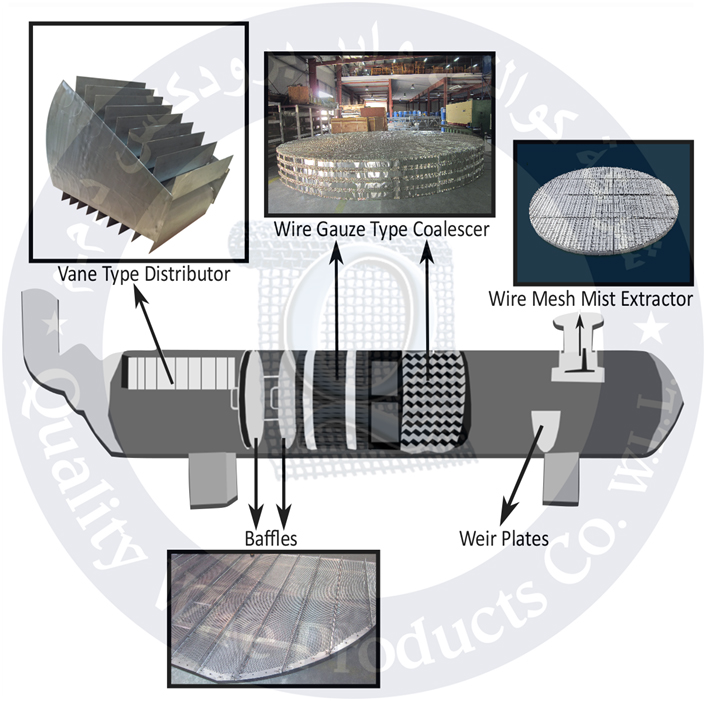
Three-Phase Separator Internals – Vane Type Inlet Device
Our company manufactures high quality Vane Type Inlet Devices, which are ideal for minimizing the ongoing momentum of the inlet stream and they also ensures a uniform distribution of the inlet stream. These devices are normally used for momentum of inlet fluids in the range of 2100 Pa to 8000 Pa. However, it is significant to take note of the fact that the material grade will be generally in stainless steel grades, as it will offer superior performance against corrosion when compared to carbon steel. The inlet device is also designed to meet the size and diameter requirements of the inlet nozzle size.
Three Phase Separator
As we mentioned above, Three Phase Separator is mainly used for the separation or segregation of the three main phases of oil, water and gas.
Features
- Catching rims are specifically designed for capturing excess liquid molecules and for reducing the re-entrainment
- Each of the row of vanes within the inlet device is efficiently wielded to a mounting strip both at the bottom and top
- The device comes with an excellent vane ladder assembly.
- Ideal choice for vessel with size more than 50mm ID
- Greater efficiency when compared to half open pipes
Three Phase Separator Internals- Perforated/Calming Baffles
Calming Baffles or Perforated baffles are commonly used in the subsequent stages of the gravity separation processes in the three phase separators. The internal of the device is efficiently designed by our manufacturers for a uniform distribution, which is of significant importance because it will quicken retention time and increase the efficiency of the entire process.
Features
- Reduced pressure drop
- Helps in even distribution of gas
- Boosts the efficiency of liquid-liquid separation
Three-Phase Separator Internals
Wave breakers or weir plates are actually plain plates that are located right under after performing a perforated baffle assembly or a perforated baffle. The main purpose of using this device is to properly synchronize the level of the heavier and lighter components. However, this device also helps in the transfer of the liquid into the corresponding liquid surge sump/tanks.
Features
- One-time installation
- Efficient and simple design
- Ideal choice for maintaining the levels of water and oil through control valves.
Process Data Sample
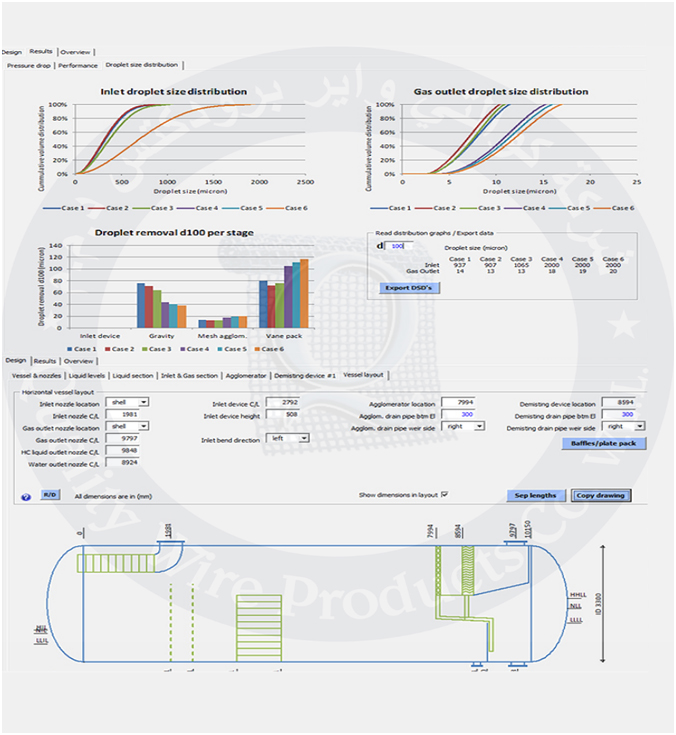